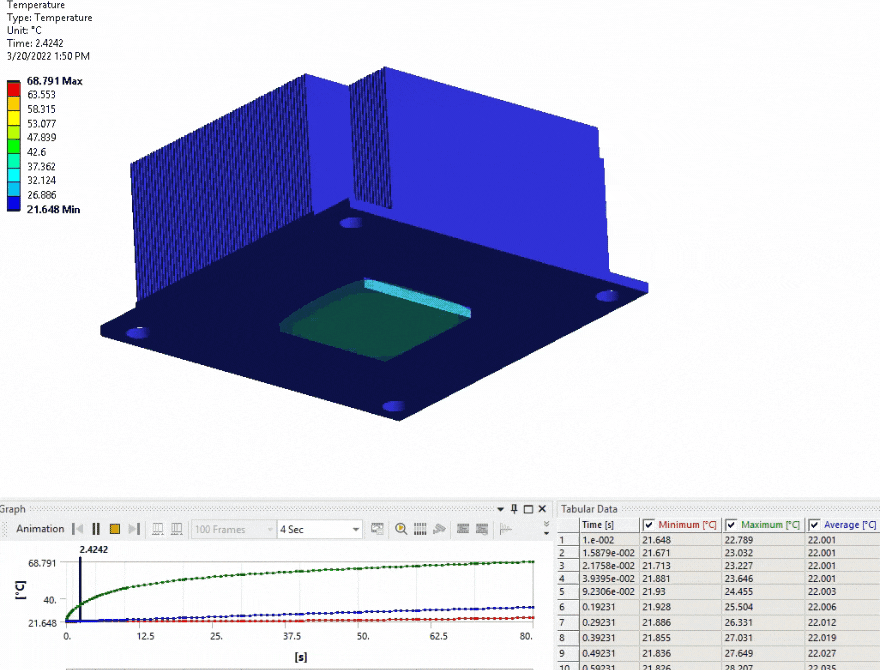
Thermal Analysis
Simulate thermal changes that occur when a system or part is heated, cooled or dissipating energy.
Simulate Thermal Behavior
Verify and Optimize
Avoid Part Failures
Capabilities
We perform
Finite Element Analysis (FEA) and Computational Fluid Dynamics (CFD)
using ANSYS software and write custom heat transfer, thermodynamic, and pressure drop codes for transient and steady-state problems.
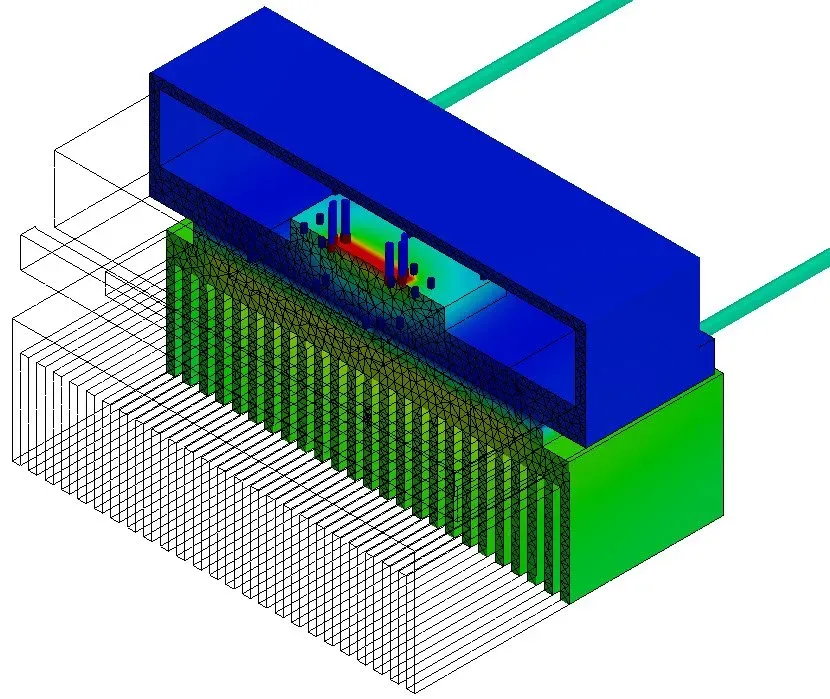
Finite Element Analysis
Thermal FEA using ANSYS to simulate temperatures using heat transfer and thermal loads.
CFD simulates velocity distribution, density, temperature, heat transfer, and fluid distribution in fluid flows.
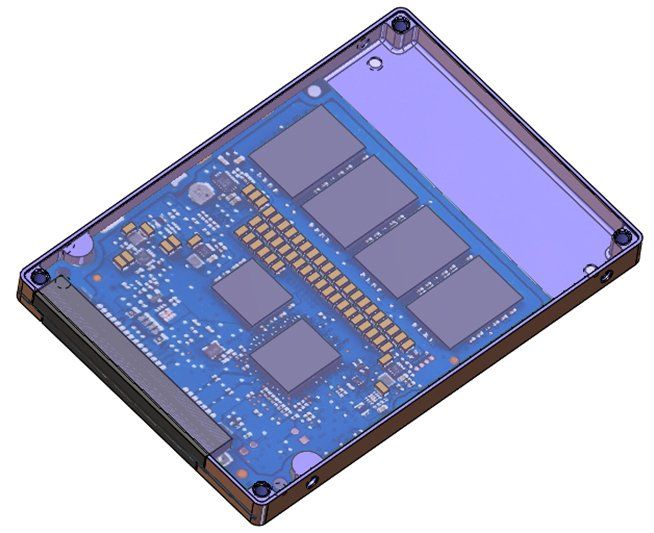
Electronics Cooling & Packaging
Simulate electronics performance under various heat loads and ambient conditions to ensure components are cooled enough to operate.
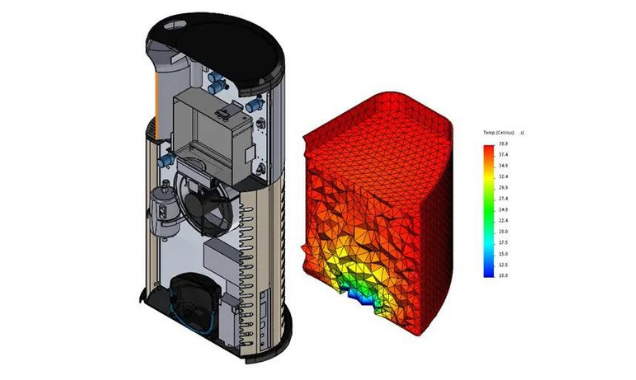
Thermal Management
Thermal management system design, fabrication, integration and test including pumped refrigerant systems, custom vapor compression systems, and single and two-phase liquid and air-cooling systems.
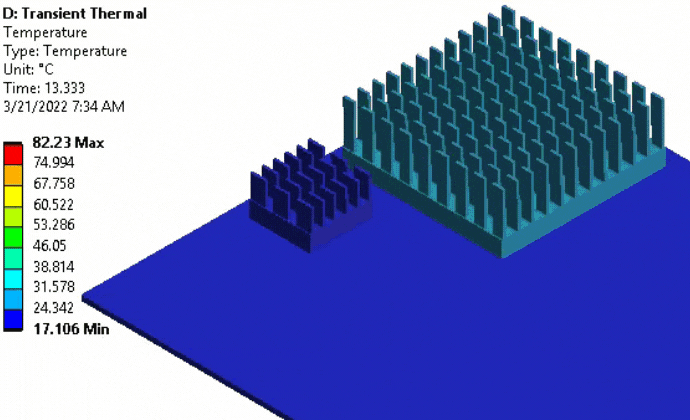
Transient Analysis
Calculate heat transfer, temperature, and flow rates under transient (time-varying) conditions.
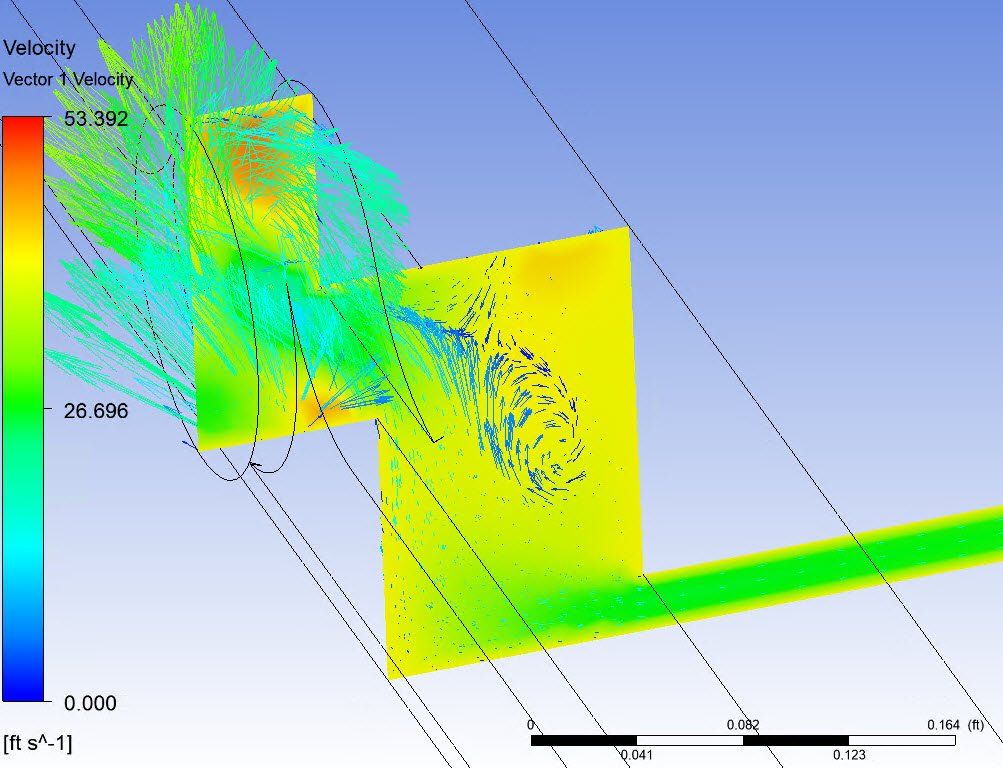
Pressure Drop Analysis
Perform pressure drop analysis, lift and drag in hydrodynamics or aerodynamics, as well as rotating turbomachinery for pumps and turbines.
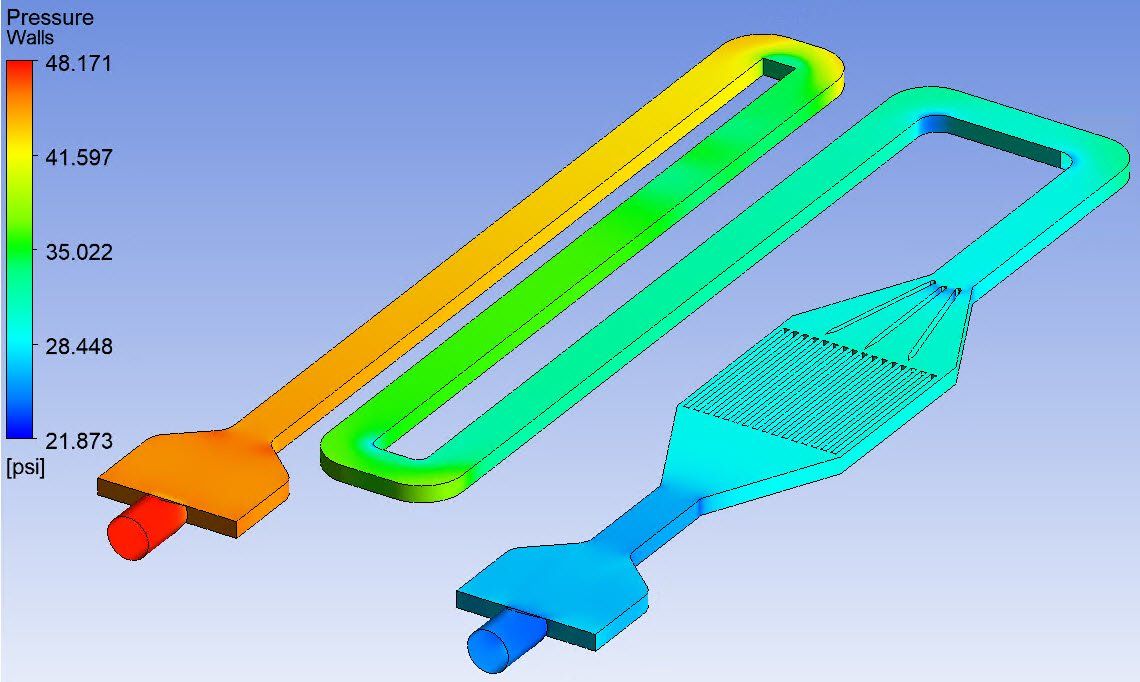
Cold Plate Design
Single & two-phase cold plate design, fabrication, integration, and test. Design of high-performance microchannel and mesochannel cold plates.
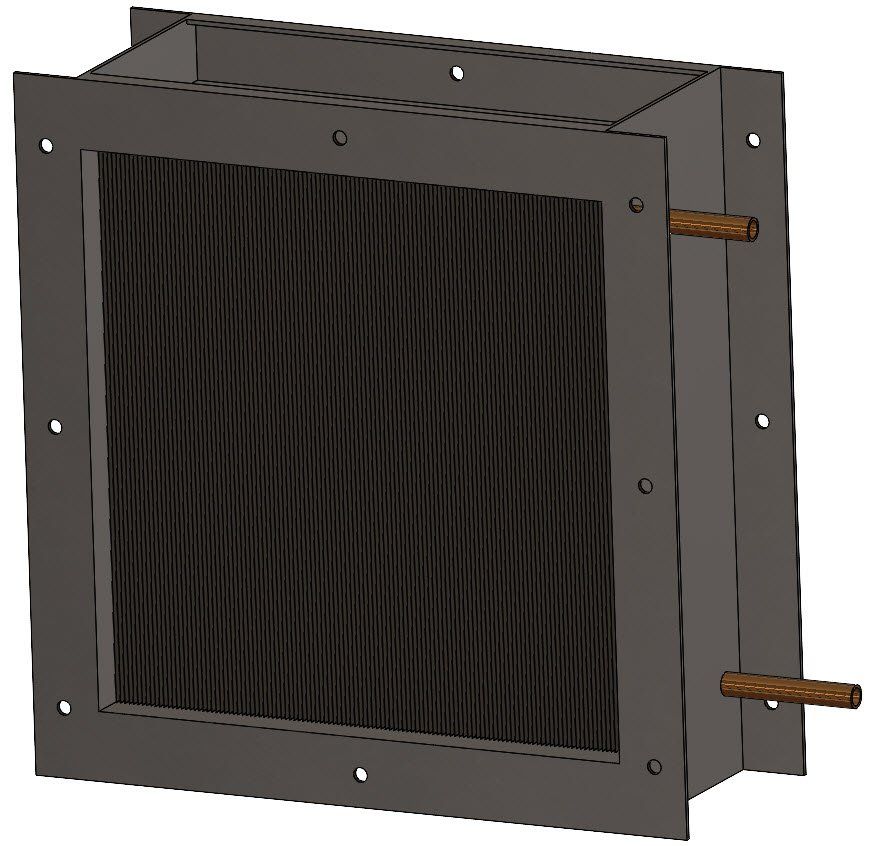
Heat Exchanger Design
Heat exchanger design including single & two-phase heat exchangers, condensers and evaporators.
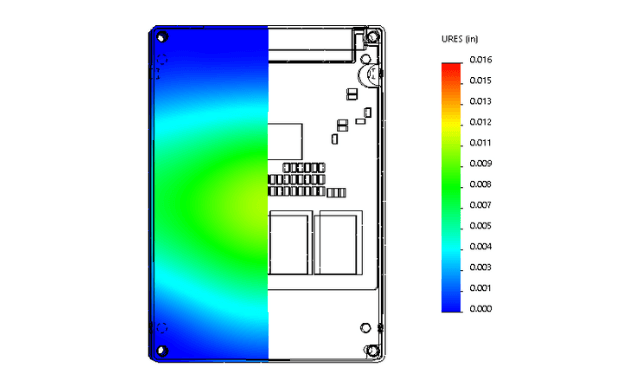
Thermal Stress Analysis
Model the thermal loads and resulting stresses within the material to identify high-stress and extreme-temperature areas that may be prone to failure.
Core Software
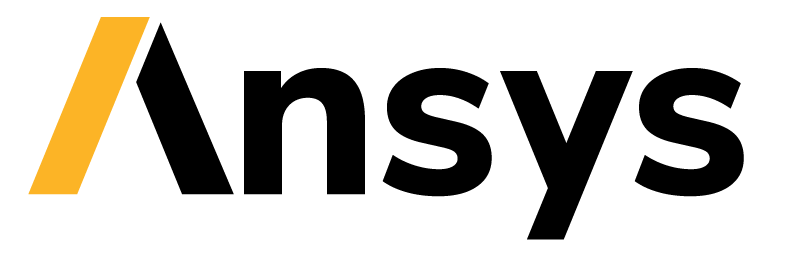
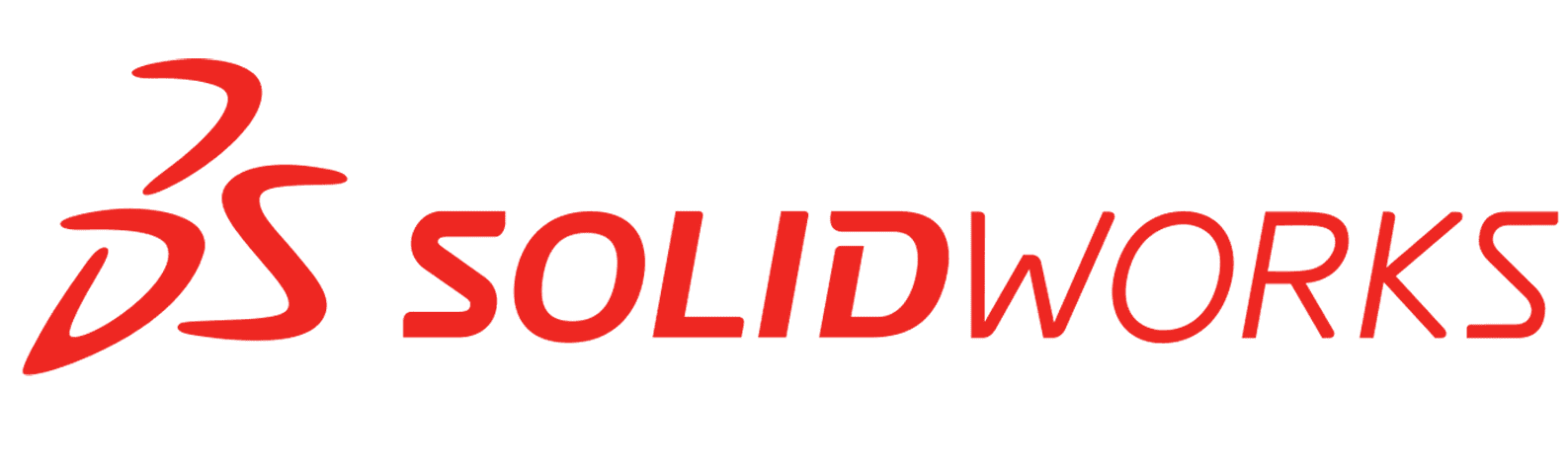
Thermal Analysis Solutions for Complex Mechanical Systems
We verify components meet requirements early in the design cycle, saving you costly and time-consuming prototype iterations.
What is Thermal Analysis?
Thermal analysis is a set of techniques used to study and understand the behavior of materials and systems in response to changes in temperature over time. It involves the measurement and analysis of thermal properties and how they change as temperature varies.
Why Use Thermal Analysis?
Thermal Analysis is used to understand and predict how heat is distributed and managed within a system or component. Thermal analysis is important when materials are exposed to high temperatures, when heat is being dissipated, or when a process requires a change in temperature. Machines, products, and devices utilizing electrical components require thermal analysis to evaluate and compare different cooling solutions (such as air cooling, liquid cooling, or heat sinks) of the electrical system.
Interested in an Analysis Quote?
We want to know your needs exactly so we can provide the perfect solution.