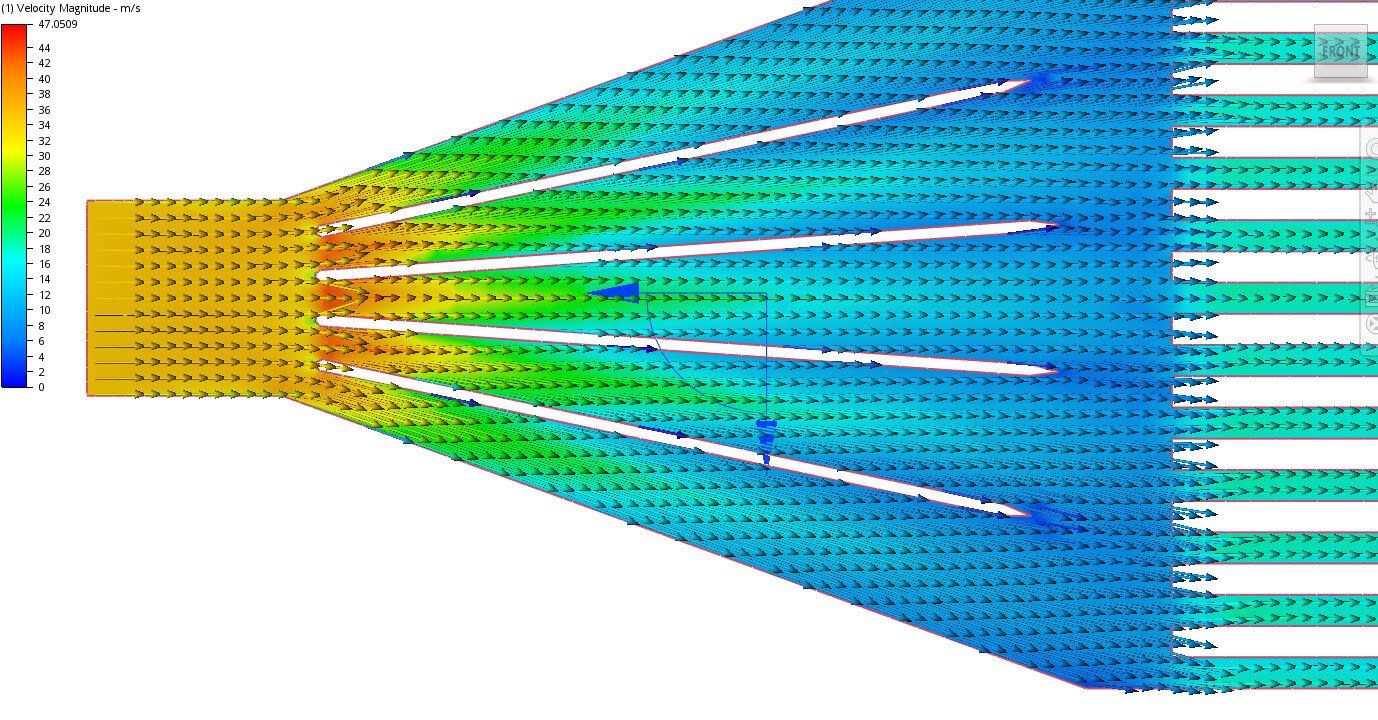
Computational Fluid Dynamics (CFD)
Numerically simulate the physics of all fluid-to-fluid and fluid-to-solid interactions in your design.
Simulate Fluid Interactions
Verify and Optimize
Avoid Part Failures
Capabilities
We provide Computational Fluid Dynamics (CFD) simulation services using ANSYS software to solve complex fluid-related problems numerically and ensure air and liquid flow in your design operate as intended.
Core Software
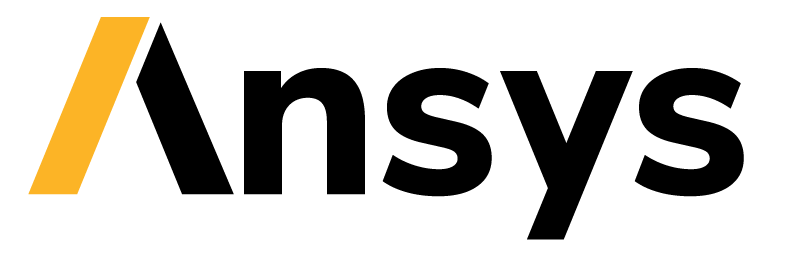
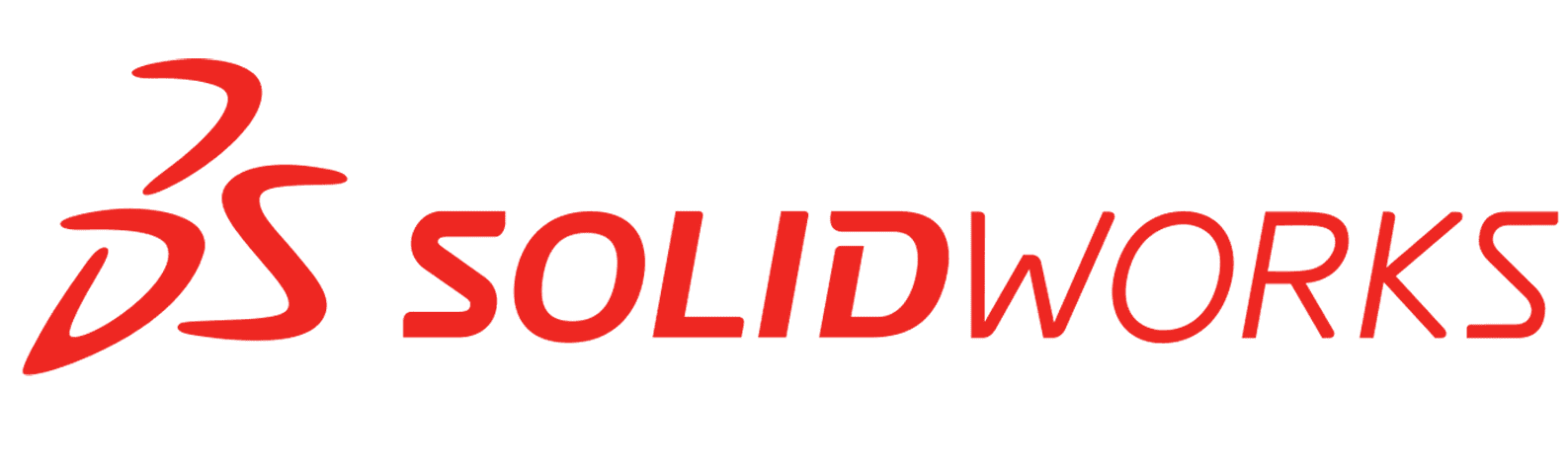
Analyzing Complex Fluid Flows with CFD
We use physics-based simulations to solve real-world problems in fluid-flow to ensure components meet requirements early in the design cycle, saving you costly and time-consuming prototype iterations.
What is Computational Fluid Dynamics (CFD)?
Computational Fluid Dynamics (CFD) is the analysis of fluid flow and heat transfer phenomena. CFD simulates the interaction of all fluid-to-fluid, fluid-to-solid, and fluid-to-gas contact, and accounts for various fluid properties, such as velocity, pressure, and temperature.
Why Use Computational Fluid Dynamics (CFD)?
Fluid flow analysis is needed when fluid interactions play a critical role in design. CFD is a valuable tool that enhances engineering design decision-making due to its accuracy and cost-effectiveness when compared to testing physical components.
Interested in an Analysis Quote?
We want to know your needs exactly so we can provide the perfect solution.