Manufacturing Process Test Fixture Design and Engineering
We designed and delivered a specialized manufacturing process development test fixture.
This fixture allows our customer to validate a new time, temperature, and pressure-dependent process without the large investment required for production hardware. This is a very inexpensive way to validate a new process and reduce risk before more expensive full-scale production machines are.
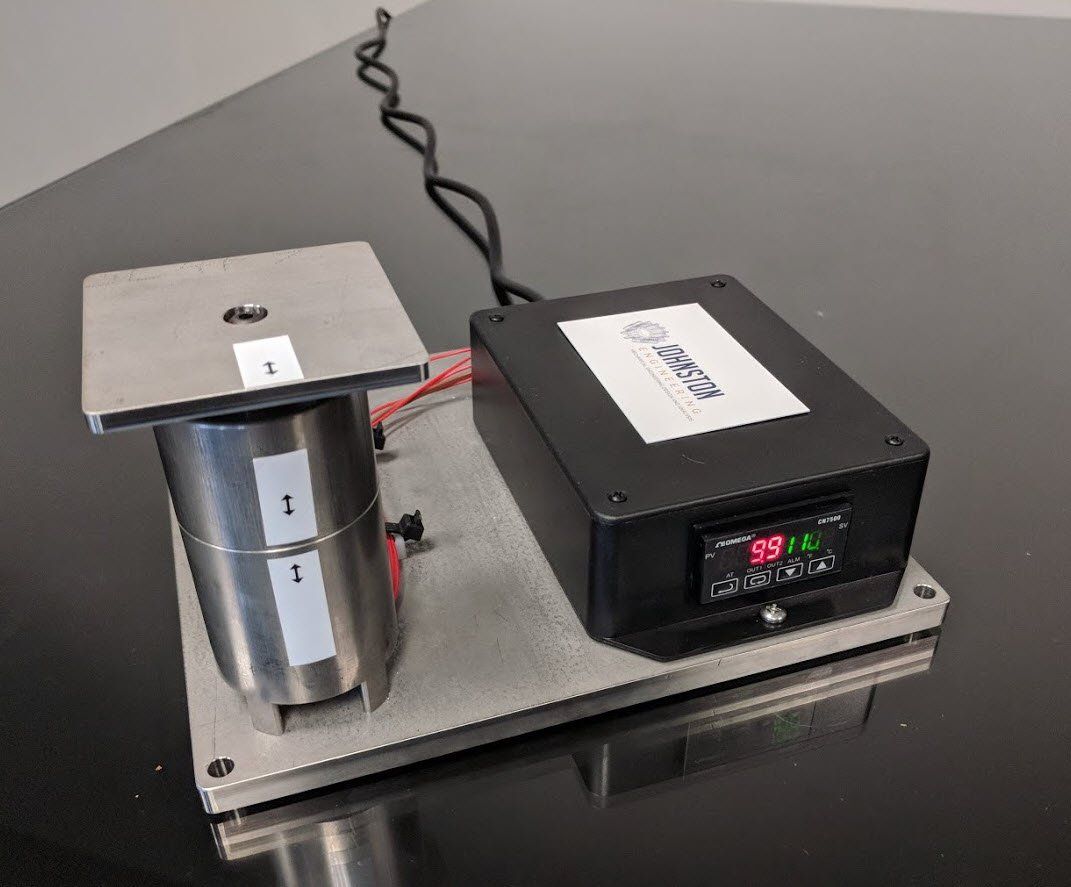
The test fixture contains cartridge heaters and a thermocouple for reading temperature. The heaters are controlled by a temperature process controller running a PID loop. The operator just sets the desired temperature setpoint and the controller ramps to and holds the temperature setpoint.
Our Contribution:
Johnston Engineering provided product development engineering design, thermal analysis, component sourcing, product build, programming, and testing to take this project from a concept sketch to a fully functioning test fixture.
- Mechanical Design
- Mechanical Engineering
- Convection Thermal Analysis
- Finite Element Analysis (FEA)
- Material Sourcing
- Material Ordering
- Product Assembly
- Product Test
3D CAD files were generated in SOLIDWORKS and reviewed with the customer to ensure the proper design intent was met. A thermal analysis study was completed to size the heaters and verify acceptable unit maximum temperature and temperature uniformity at the process area. The study required calculating a natural convection heat transfer coefficient to determine the heat lost from the fixture. The heat transfer coefficient is one of the inputs used to complete a thermal Finite Element Analysis (FEA) study using ANSYS as shown in [Figure 2]. The thermal FEA was completed by iterating the heater input power and heat loss calculations until both maximum temperature and temperature uniformity are acceptable at a heat input value that can be achieved with off-the-shelf heaters. These results were then used to select appropriate heaters.
Then, drawings were generated, and all machined parts were fabricated by a local machine shop. The components were assembled, and the controller was programmed to achieve the desired temperature setpoint without overshoot. Finally, the fixture was tested to validate performance before delivering to the customer for process development testing
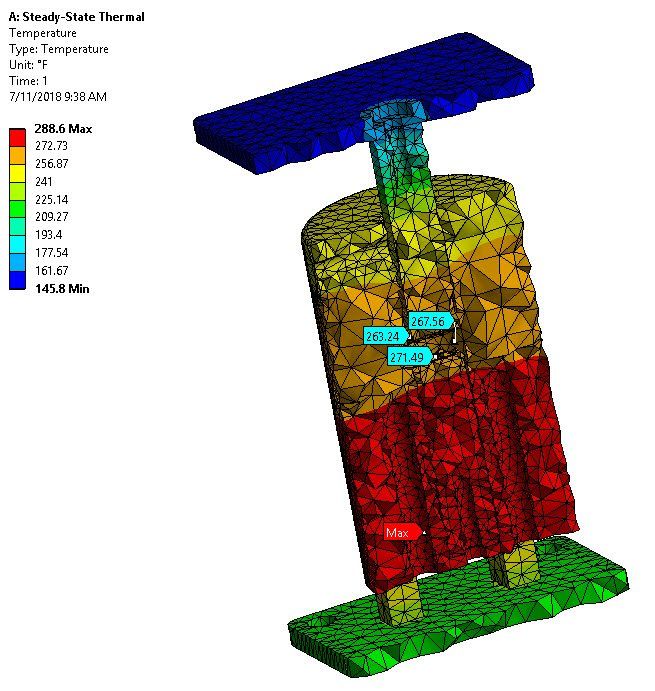
[Figure 2]
Thermal FEA temperature plot results show acceptable maximum temperature and temperature uniformity.